SEMT Insert: Achieve Optimal Surface Finish and Chip Control Details
Product Information:
SEMT insert square shape face milling insert. Face milling produces flat surfaces and machines work to the required length. In face milling, the feed can be either horizontal or vertical. SEMT insert geometry is calculated for maximum cutting efficiency. Four cutting edges allow you to rotate the insert for four times the life.
Specifications:
Type | Ap (mm) | Fn (mm/rev) | CVD | PVD |
VT3020 | VT3040 | VT1025 | VT1325 | VT1525 | VT1328 | VY1010 | VY1520 | VY1525 | VY1028 | VY1330 |
SEMT1204AFTN-GM | 3.00-8.50 | 0.09-0.16 |
|
| • | • | O | O |
|
|
|
|
|
• : Recommended Grade
O: Optional Grade
Application:
It suitable for most materials.Mainly focuses on face milling and cavity profile milling of steel alloy steel, stainless steel and cast iron.
FAQ:
What are face mills?
Face milling is a machining process in which the milling cutting is placed perpendicular to the workpiece. The milling cutting is essentially positioned “face down” towards the top of the workpiece. When engaged, the top of the milling cutting grinds away at the top of the workpiece to remove some of its material.
What is the difference between face milling and end milling?
These are two of the most prevalent milling operations, each using different types of cutters – the and mill and the face mill. The difference between end milling and face milling is that an end mill uses both the end and the sides of the cutter, whereas face milling is used for horizontal cutting.
Our Company
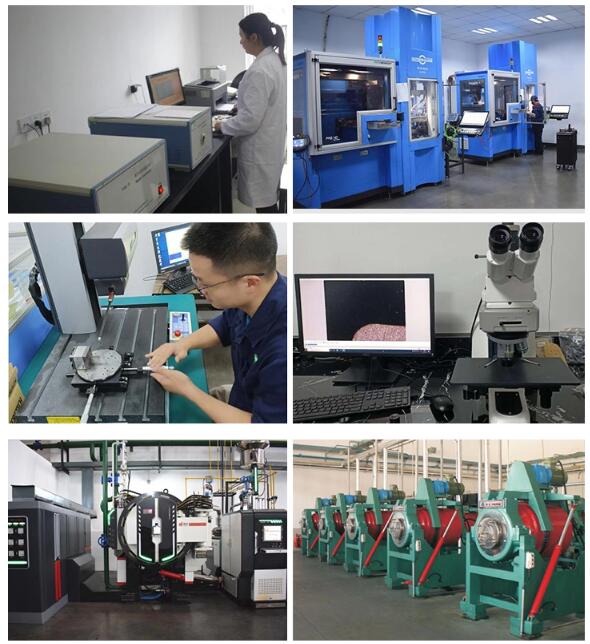
Package Shipment
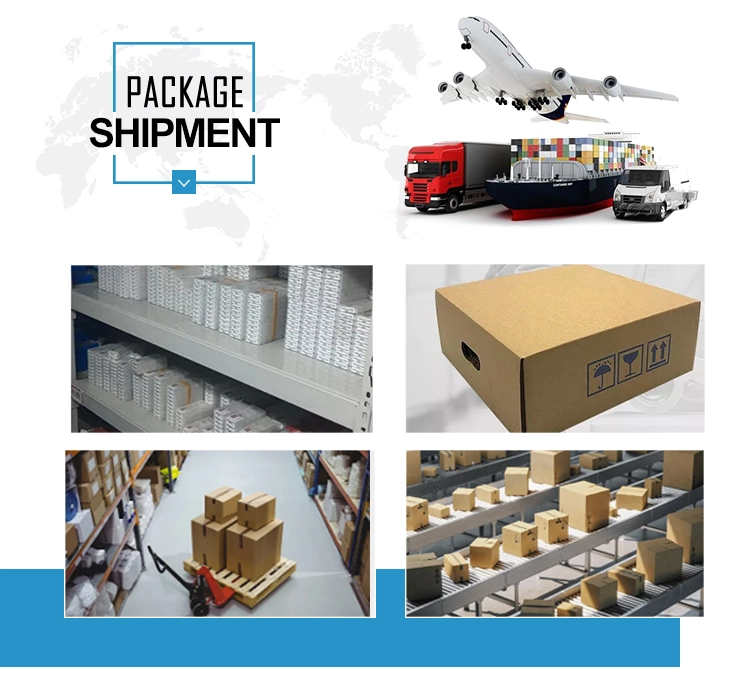